Application 2. 225 MW Steam Turbine Assemblies
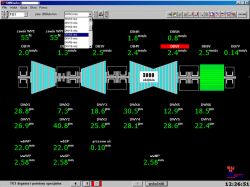
n its final configuration, the system will be installed on eight large steam turbine assemblies, 225MW each. At present (July 2005), six machines are covered by the system's operation. Due to numerous vibration channels, the TNC2000 set of each machine is provided with the JAD32/32 data acquisition unit. The system's functionality ensures supervision and protection, operation visualisation, diagnostics and data recording. The VMSH type modules employed for the measurement of relative vibrations offer additional protection against fluctuations of vectors 1X and 2X. The measurements performed on each machine include: - 9 absolute vibration channels to measure frequency in two axes for selected bearings - 12 relative vibration channels, six bearings in two axes - eccentricity - 2 channels for measurements of axial movement - 3 channels for bearing mount absolute thermal expansion - 3 channels for relative expansion - 2 channels for measurement of valve opening - speed measurement (rpm) - phase marker An interesting diagnostic case, as described below, was observed shortly after installation of the system on the first machine. The dynamic behaviour of the machine was rather not good. High periodical vibrations were observed on the turbine bearings, especially on bearing no.1. It was noted that in the higher ranges of power, the shaft in no.1 bearing was subjected to vibrations having frequency equal to ½ fo and an amplitude exceeding that of fo. The installed system made it possible to directly monitor the shaft's behaviour in all its bearings (real-time observation of trajectory and spectrum). It was further noted that a disturbance of the oil wedge preceded directly the appearance of the ½ fo frequency (frequency range 23-35 Hz). The operation was then becoming unsteady, resulting in violent vibrations about 25 Hz. Such phenomena were observed mainly for bearing no. 1 and 3. It should be noted that the said disturbance of oil wedge is rather hard to disclose by analysis of the registered data base. The instability in operation can, however, clearly be seen by the real-time observation of the trajectory.
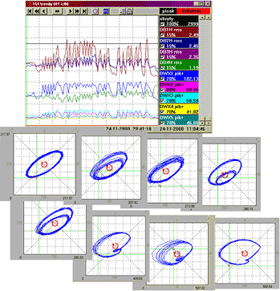
It might have therefore been presumed that it is the disturbance of the oil wedge that is responsible for the excitement of the resonant frequencies. However, a question which remains is why such disturbance is generated in higher ranges of power only. Maybe it can be contributed to a decrease in the bearing load. An analysis of shaft position, its trajectory and vector of vibrations for all bearings has been conducted. Basing on the readings of the relative vibration sensors during machine and foundation cooling down, an analysis of the thermal expansion of the bearing mounts has also been made. The conclusion presented itself by its own. The experienced problem was not due to the fault of no.1 bearing but it was rather caused by the shaft misalignment on the machine reaching its normal operation temperature. Accordingly, the positions of bearings no. 3 and 4 were adjusted, whereby a positive improvement of the machine's dynamic behaviour was achieved.